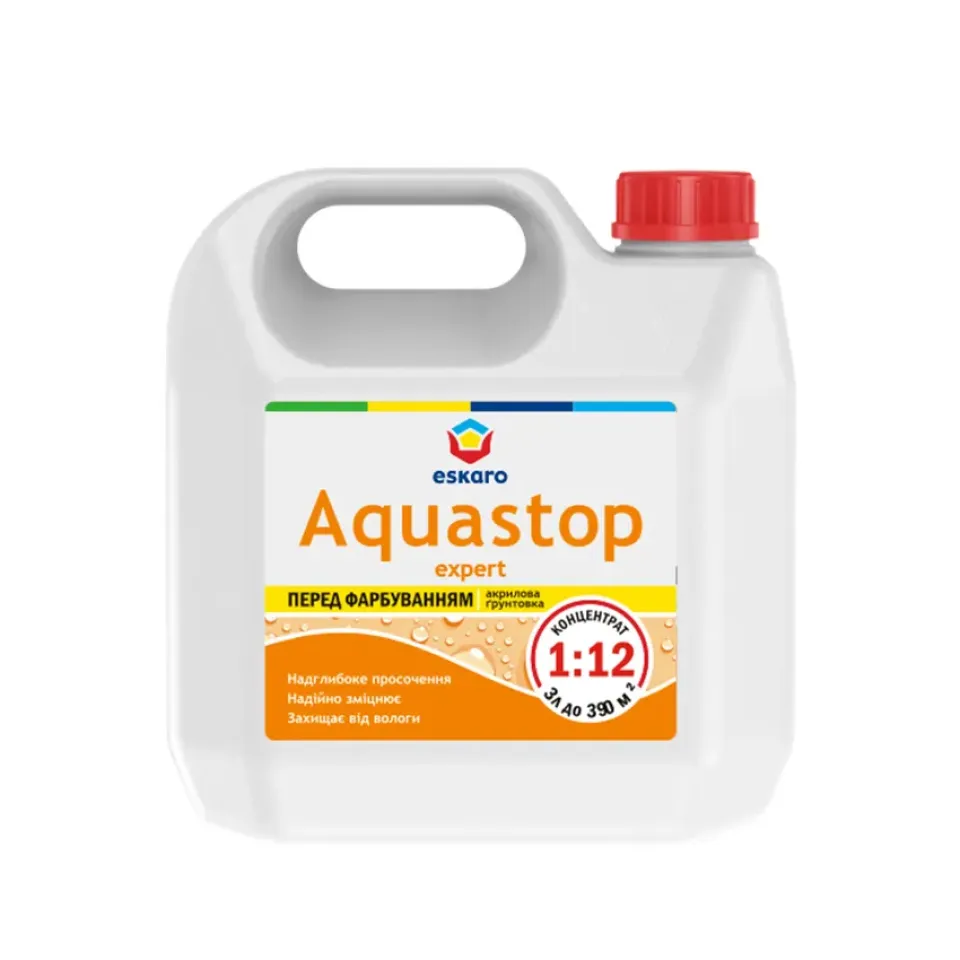
Advantages of water-dispersion penetrating primer concentrates over ready-made primers.
The main purpose of any primer is to prepare the surface before applying further material.
During repair and construction work, many different materials are used, which are called the word "primer". Therefore, the purpose and scope of application of these primers determine their properties and composition.
Next, we will consider only one type of primer, namely, permeable water-dispersion primers, which are intended for general construction work, such as surface preparation before applying plaster, putty, tile adhesive, water-dispersion paint, etc.
Penetrating water-dispersion primers presented on the Ukrainian repair and construction materials market can be divided into two main groups, which differ in the degree of concentration:
1. Ready-to-use primers.
2. Primer concentrates.
Before buying a primer, the consumer has a question: what is better to buy: a ready-made primer or a primer concentrate?
To answer this question, it is necessary to understand in more detail the composition and properties of both groups of primers, as well as their areas of application.
Purpose and composition of permeable water-dispersion primers
A permeable primer strengthens the surface and also reduces (and evens out) its absorbency.
A permeable water-dispersion primer consists of two main components: latex dispersion and water. Latex dispersion is a binder (adhesive, reinforcing) substance, and water is a diluent (with which the latex dispersion is distributed over the surface).
Latex dispersions in primers can be acrylic or styrene-acrylic. On labels and in technical sheets, as a rule, both are called “acrylic”. In addition, these dispersions can be additionally modified with silicone resins, in which case such primers on labels and in technical sheets can be called “silicone”.
What is the fundamental difference between the products: ready-made primer and concentrate primer?
Let's consider the option when both products are made from the same raw material (dispersion). In this case, the primers differ only in the amount of latex dispersion per unit volume of the product, which is packaged in consumer packaging. And in order to get a finished primer from a primer-concentrate, the concentrate must be diluted with water.
When a primer-concentrate is diluted with water (in the proportion recommended by the manufacturer), a finished primer is obtained.
One of the most important properties that characterize the quality of a primer is its dry residue. The dry residue of a primer is the "solid substance" that remains from the primer after the solvent - water - evaporates from it.
The dry residue in the primer is only in latex dispersion (and in silicone resin, if the primer is modified with it). It is their amount in the primer that determines its dry residue.
The dry residue of the primer is measured in percent. For example, if after drying 100 grams of primer, 5 grams of dry matter remain, then the dry residue of the primer is 5%. If 8 grams remain, then 8%, if 2.5 grams, then 2.5%.
A very important indicator for the primer is the size of the molecules of the dispersion from which it is made. For the most part, acrylic dispersions have a 2-3 times smaller dispersion molecule size compared to the size of the molecules of styrene-acrylic dispersions. But at the same time, acrylic dispersions are more than 1.5 times more expensive than styrene-acrylic ones.
If we compare two primers with the same binder but different dry residue, it will turn out that at the same consumption (in m2/l) on the same types of surfaces, the primer with a higher dry residue will strengthen the surface better (and reduce its absorption capacity). Conversely, in order to qualitatively strengthen the surface, the amount (volume) of primer with a lower dry residue is required more, because the surface will have to be primed more times in order to strengthen (“saturate”) the base with a sufficient amount of “dry residue”.
If we compare two primers with different molecular sizes and the same dry residue, then at the same consumption (in m2/l) on the same types of surfaces it will turn out that the primer with a smaller molecular size will strengthen the surface better.
That is why primers with a small molecular size (from acrylic dispersion) are recommended for use in more critical areas of repair and construction work.
Further in the text, we will consider the comparison of ready-made primers with concentrate primers only with respect to products based on styrene-acrylic dispersion not modified with silicone resins.
What dry residue should a “quality” ready-made primer have? Practice shows that a quality primer should have a dry residue of approximately 5–6%. This is the dry residue of ready-made primers offered on the market by serious manufacturers of paint and varnish products and manufacturers of dry mixes.
In order to make ready-made primers more attractive in terms of cost to the buyer, some manufacturers reduce the cost of primers simply by reducing the amount of latex dispersion (binder) in them, which automatically leads to a decrease in their strengthening ability. Most often, such primers are used for irresponsible work.
We will not give examples of specific products and manufacturers, but we note that on the Ukrainian market of building materials there are inexpensive ready-made "primers", in which the dry residue when tested is 1.5% and even 0.8%.
In the vast majority of cases, manufacturers do not indicate the amount of dry residue of their primers, so the consumer has the opportunity to assess their quality only after application.
Types and properties of surfaces.
What are the types of surfaces (and the degree of absorption and strength) that require preparation with a penetrating water-dispersion primer?
Note: If the surface is non-absorbent, then a penetrating primer cannot be used to prepare it.
There are three main categories of surfaces (according to the degree of absorption and strength):
- 1. Highly absorbent (weak or very porous) surfaces: shell rock, aerated concrete, foam concrete, cement-sand plasters with a low cement content, gypsum, alabaster.
- 2. Medium absorbent (fairly strong) surfaces: plasterboard, cement-sand plasters, concrete, red brick, silicate brick, fiberboard, chipboard, MDF.
- 3. Low-absorbent (very strong, dense non-porous) surfaces: heavy concrete, natural stone (flagstone, sandstone, etc.).
Features of priming surfaces of different (by degree of absorption and strength) categories.
For priming different (by degree of absorption and strength) categories of surfaces, it is necessary to use primers with different amounts of dry residue.
There is a general rule when priming a surface with a penetrating primer:
The more absorbent and less durable the surface, the higher the dry residue the penetrating primer should contain. Conversely, the less absorbent and more durable the surface, the lower the dry residue the penetrating primer should contain. A properly primed surface must meet the following requirements::
- 1. There should be no visible solid shiny film on the surface. The film is a sign of surface re-priming and negatively affects the adhesion of subsequent material.
- 2. After passing the palm of your hand with light pressure on the surface - nothing should fall off the surface, and the palm should remain clean, without traces of dust, chalk, etc. If anything falls off or the palm is dirty, then the surface is not primed.
- 3. A drop of water applied to the surface should not be absorbed into it within 30–40 seconds. After this time, the water should be absorbed by the surface. If the drop of water is immediately absorbed into the surface, then the surface is not primed.
If after applying one layer of penetrating primer the surface appears:
- - if it is not primed, it must be primed again.
- - if it is overprimed, it is necessary to completely remove the continuous shiny film from it mechanically.
In both cases, it will be necessary to spend additional time, effort, and materials to bring the surface to a state of "proper grounding."
Використання готової ґрунтовки.
In the case of using a ready-made primer (when applying one layer of primer), there is a high probability of both under-priming the surface and over-priming it.
To reduce the time of work on the site, the number of technological “approaches” to the treated surface should be reduced to a minimum. That is, priming the same surface, as one of the stages of work, should be performed at one time.
Let's imagine that the ready-made primer contains a small amount of dry residue, and it is necessary to prime a highly absorbent, weak surface. In this case, the surface will have to be primed in at least 2 layers, and you will have to wait several hours for the surface to dry between layers.
Let's imagine the opposite situation, when there is a high-quality ready-made primer with a large amount of dry residue, but it is necessary to prime a weakly absorbent, very strong surface. In this case, after priming, a film is necessarily formed on the surface, which will need to be removed mechanically. In order not to over-prime the surface with the finished primer when applying it in one layer, the primer will need to be diluted with water before application to reduce the amount of dry residue.
Using a primer concentrate.
The most important advantage of a concentrated primer compared to a ready-made primer is that using a concentrated primer, you can guarantee to prime any surface category “in one go”, that is, by applying only one layer of primer.
To do this, you need to assess the surface category, and taking this into account, dilute the concentrated primer with water (which is available at any construction or repair site) in the proportion specified by the manufacturer. Then the prepared (diluted) primer is applied to the surface with the consumption specified by the manufacturer.
For example, it is necessary to prime a concrete surface using a concentrated primer. In this case, the label of the concentrated primer states: “for priming concrete (medium-absorbent surface), dilute the concentrated primer with water in a ratio of 1:7, and then treat the surface with the prepared solution at a consumption of 6–8 m2/l”.
To correctly calculate the consumption and prepare the finished primer from the primer concentrate, you need to:
- 1. Add seven liters of water to one liter of the primer concentrate. The result is eight liters of the finished primer.
- 2. This amount of primer (8 liters) will be enough for high-quality priming from 48 to 64 square meters of concrete surface with a consumption of 6–8 m2/l.
Some manufacturers indicate the consumption and degree of dilution of the primer concentrate in the form of a convenient table for calculation.
An example of such a table for the Aura AquaGrund primer concentrate:
Surface absorption
strong | average | weak | |
Material | gypsum, aerated concrete foam concrete, shell rock | plaster, concrete, brick, gypsum plasterboard, fiberboard, chipboard | stone, dense concrete |
dilution primer- concentrate/water | 1:5 | 1:7 | 1:10 |
quantity of ready-made primer from 1l of primer concentrate | 6л | 8л | 11л |
consumption of diluted primer | 3-4 м²/л | 6-8 м²/л | 9-10 м²/л |
consumption of primer-concentrate | до 24 м²/л | до 64 м²/л | до 110 м²/л |
Other additional advantages of a concentrated primer compared to a ready-made primer:
- - less space is required for storage.
- - less costs are required for transportation.
- - no need to pay for the diluent - water, which is contained in the ready-made primer.
- - no need to pay for the additional volume of containers required for storing the ready-made primer.
- - the cost of one liter of ready-made primer (with the required amount of dry residue) obtained from a concentrated primer is always guaranteed to be less than the cost of one liter of ready-made primer (with the same required amount of dry residue), but all this is provided that the ready-made primer and the concentrated primer are made from the same dispersion.
In order to assess the economic advantage of a concentrated primer over a ready-made primer, it is necessary to calculate the cost of one liter of primer prepared from a concentrated primer and compare it with the cost of one liter of a ready-made primer.
Here is an example of such a calculation and comparison:
Let the volume of a bottle with a concentrated primer "1:10" be one liter and its cost is 121 UAH, and the volume of a canister with a ready-made primer is 10 liters and its cost is 220 UAH.
1 liter of a concentrated primer "1:10" will yield 11 liters of ready-made primer, while the cost of one liter of ready-made primer will be: "121 UAH: 11 l = 11 UAH/l".
The cost of one liter of ready-made primer will be: "220 UAH: 10 l = 22 UAH/l".
11 UAH/l is definitely less than 22 UAH/l, which means it is more economical to buy a concentrate primer compared to a ready-made primer.
Considering all of the above, for the end consumer, concentrate primers are a more profitable purchase than ready-made primers.